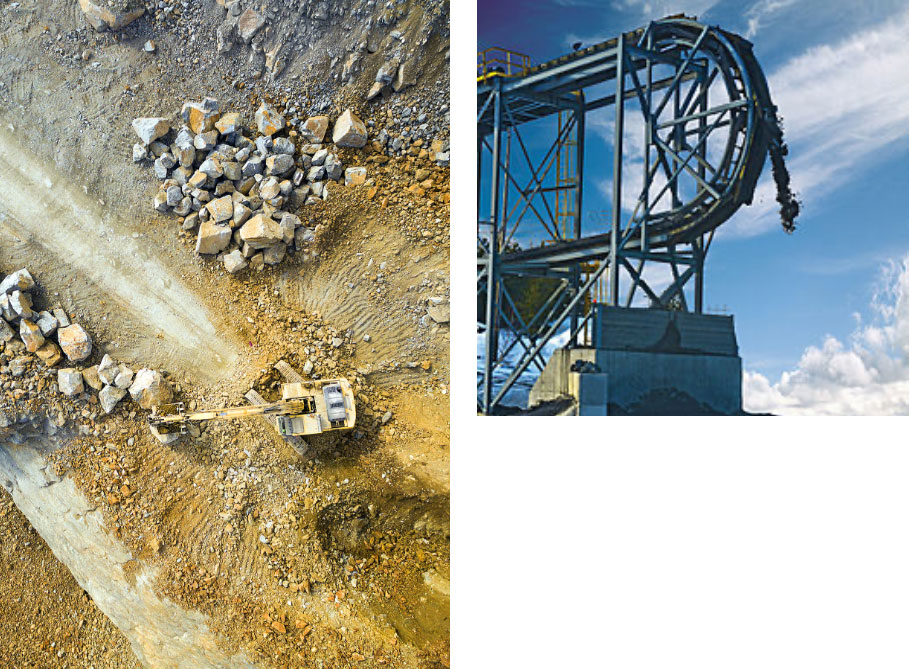
Design & Engineering
Mining is not a one-size-fits-all proposition. The configuration of each mine is different – and so are the challenges facing mine owners when it comes to hauling materials from the face and streamlining those processes. It is for this reason that Railveyor designs, installs and services each material handing system on a fully customized basis.
The front end of our process is driven by detailed site surveys and exhaustive engineering over an 8-16 week time frame to customize the application of Railveyor’s ground-breaking, innovative technology. We work closely with mine company engineers – not only to make sure we’re solving the right problems and leveraging the right opportunities – but to help our mining client’s staff fully understand the fundamentals of the material hauling system that will be installed in their mine. In a very real sense, we create the system specifications together in a symbiotic interplay of problems and solutions.